智慧赋能高效协同的全能制造ERP管理软件系统
19429202025-03-25教程攻略13 浏览
1. 传统ERP为何难以应对现代制造的“协同之痛”?
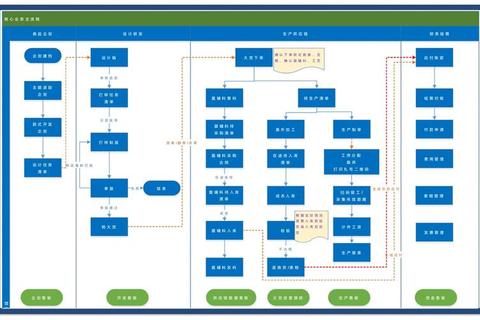
当某知名汽车零部件企业因订单临时变更导致500万库存积压时,其德国总部CIO无奈承认:“我们的ERP系统就像被锁在保险箱里的账本,生产、采购、销售部门始终在用不同版本的数据对话。”这个案例暴露出传统制造管理的致命短板——信息孤岛严重、协同效率低下。据Gartner统计,全球67%制造企业因系统割裂导致的协同成本,吞噬了至少15%的利润空间。
智慧赋能高效协同的全能制造ERP管理软件系统正是破解这一困局的钥匙。这类系统通过物联网与AI技术的深度融合,正在重塑制造业的价值链条。以金蝶云·星空为例,其多工厂协同模块帮助葆德空压机实现跨6省生产基地的产能动态调配,订单交付周期缩短40%,库存周转率提升至行业平均水平的2.3倍。这种打破物理边界的实时协同能力,让传统ERP望尘莫及。
2. 如何让计划与生产“同频共振”?
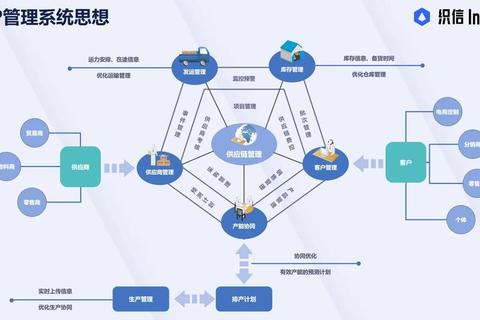
河北耀讯新能源曾因计划排产失误导致3000万储能设备延期交付。引入智邦一体化ERP后,通过弹性计划体系与MES系统的深度集成,实现从原材料采购到车间工位的全链路可视化。系统自动计算的物料齐套率从68%跃升至95%,异常响应时间由72小时压缩至4小时。这印证了智慧赋能高效协同的全能制造ERP管理软件系统的核心优势:将计划准确率转化为真金白银。
这类系统的智能算法正在创造新的可能。重庆某机械厂应用忽米云ERP后,系统根据设备状态、人员技能、物料供给等12个维度自动生成动态排程,使设备利用率从65%提升至89%,产品缺陷率由18%降至10%。更值得关注的是,系统通过深度学习持续优化排产模型,每次版本迭代都能带来3-5%的效率提升。
3. 质量追溯能否从“事后追责”变为“事前预防”?
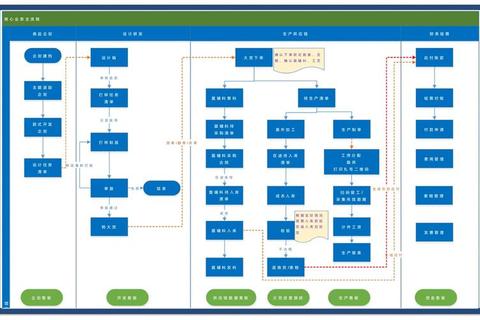
飞毛腿电池的涅槃重生故事最具说服力。火灾事故后,其ERP系统完整还原了3800种物料的流向图谱,使得2.2亿损失的定损周期从行业平均的18个月缩短至5个月。智慧赋能高效协同的全能制造ERP管理软件系统的质量模块,已进化出预测性质控能力。江苏盛捷昌的智能仓储设备生产中,系统通过关联2000多个传感器数据,在焊接工序就识别出73%的潜在缺陷,每年避免质量损失超800万元。
这种变革正在重构质量成本结构。某军工企业应用金蝶制造云后,通过工序级质量数据埋点,使废品率下降12个百分点,仅此一项年节约成本2600万。更关键的是,系统建立的26万组工艺参数关系矩阵,为新产品质量预测提供了数据基石。
从“能用”到“慧用”的进化路径
当某家电企业用ERP的机器学习模块分析出包装箱尺寸误差导致年损480万时,其总经理感叹:“这不是软件,是请了200个数字工程师。”对于制造企业,建议采取三步走策略:首先选择支持多组织架构的云原生系统,如金蝶云·星空的多工厂协同模块;其次建立跨部门数据委员会,确保87%以上业务数据接入主系统;最后培养既懂制造又通数据的复合型人才,这是系统价值放大的关键杠杆。
智慧赋能高效协同的全能制造ERP管理软件系统正在证明:当生产数据流动速度超过物料流动速度时,制造业就能突破物理世界的效率极限。那些率先实现“数据炼钢”的企业,已在这场转型中抢占了新赛道的起跑线。