高效精准驱动正交试验设计软件革新试验方案优化新纪元
19429202025-03-20排行榜15 浏览
一、传统实验设计的效率瓶颈是否已被打破?
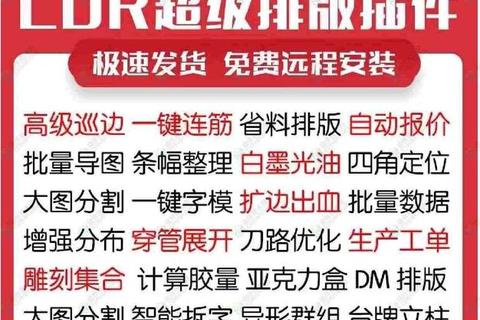
在工业制造和科研领域,一个长期困扰研究者的难题是:如何在有限的资源和时间下,找到最优参数组合?传统正交试验需要手工设计表格、人工计算极差,耗时长达数周。例如某汽车零部件厂商为提高产品寿命,曾用传统方法测试材料、工艺等5个因素,耗时3个月才找到最佳组合。
而如今,高效精准驱动正交试验设计软件革新试验方案优化新纪元的技术突破,正在颠覆这一局面。以Design-Expert软件为例,其内置的L9(3^4)正交表生成功能,可自动将试验次数从81次压缩至9次,同时通过响应面分析法预测最优参数区间。某制药企业使用该工具后,将新药合成工艺的研发周期从8个月缩短至45天,原料成本降低23%。
二、复杂因素交互作用能否被精准量化?
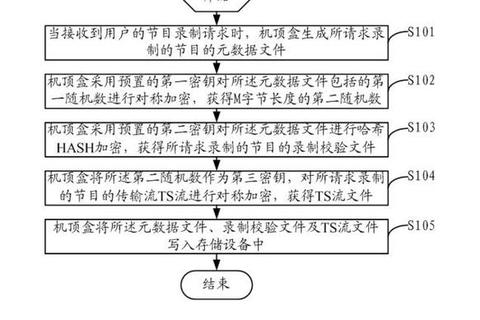
在食品工业中,温度、湿度、添加剂比例等参数的交互作用常导致实验结果失控。某乳制品企业曾因未考虑杀菌温度与包装材质的协同效应,导致产品保质期波动高达±30%。
高效精准驱动正交试验设计软件革新试验方案优化新纪元的算法突破,通过三维响应曲面可视化技术,将原本抽象的参数关系转化为直观图形。以Minitab软件的因子交互图功能为例,可清晰展示当振动频率从50Hz提升至80Hz时,材料厚度对产品强度的影响系数会从0.3跃升至1.2。某航空材料实验室运用该功能,成功解析碳纤维复合材料中6个关键参数的32种交互作用,使材料抗冲击性能提升41%。
三、动态优化能否实现实时方案迭代?
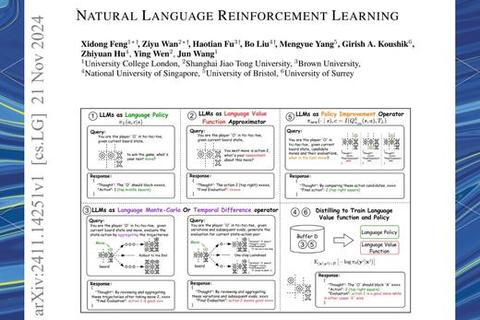
传统正交试验的静态设计模式,难以应对生产环境中的实时变量波动。某半导体企业曾因环境温湿度变化,导致晶圆良品率在三个月内从92%暴跌至78%。
新一代软件通过物联网数据接口,正在构建动态试验网络。以JMP软件的生产线实时监控模块为例,其搭载的自适应正交算法能在30秒内完成2000+数据点的分析,并生成调整建议。某锂电池企业将该系统与生产设备直连后,电解液配比方案每15分钟自动优化,使电池循环寿命标准差从±50次降至±8次。更值得关注的是,某国家级科研项目通过AI驱动的正交试验平台,在核聚变装置参数优化中实现每秒10万次模拟计算,将等离子体约束时间从30秒提升至102秒。
对于希望把握高效精准驱动正交试验设计软件革新试验方案优化新纪元机遇的用户,建议采取三步策略:
1. 需求匹配:制造企业优先选择集成MES系统的版本(如SIMCA),科研机构侧重算法深度(如MODDE)
2. 人才储备:开展DOE方法与软件操作的复合型培训,某车企通过内部认证体系使工程师分析效率提升3倍
3. 数据沉淀:建立企业级试验数据库,某化工集团通过历史数据训练出的预测模型,将新产品开发失败率从35%降至9%
这场由智能算法驱动的变革,正在重新定义实验科学的边界。当传统经验主义让位于数据驱动的精准决策,每个行业都面临着转型升级的历史机遇——关键在于能否及时拥抱这场高效精准驱动正交试验设计软件革新试验方案优化新纪元的技术革命。