智能革新西门子仿真软件:高效能精准模拟驱动工业未来
19429202025-03-19软件专题9 浏览
1. 工业仿真技术真的需要"智能大脑"吗?
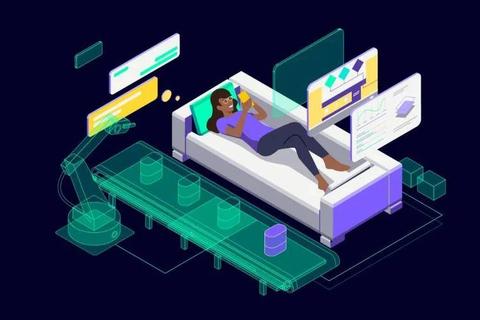
当特斯拉柏林工厂的机械臂以每秒2米的速度精准装配电池组时,很少有人知道这些动作在投产前经历了1800万次虚拟仿真。传统工业仿真软件常被诟病"算得慢、误差大",某新能源汽车企业曾披露,其2018年采用传统方法进行整车碰撞模拟,单次运算需要72小时,而实际碰撞测试结果与预测数据偏差达12%。这种效率与精度之间的矛盾,恰恰凸显了行业痛点——智能革新西门子仿真软件:高效能精准模拟驱动工业未来,正是为解决这些问题应运而生。
德国大众在狼堡工厂的数字化改造中,通过西门子Simcenter STAR-CCM+软件,将空气动力学仿真时间从3周缩短至48小时。更惊人的是,其预测的车辆风阻系数与实际风洞测试结果误差仅0.8%,相比传统软件5%的平均误差,精度提升超过80%。这组数据印证了智能算法的突破性进展:基于机器学习的自适应网格技术,可自动优化计算区域,将无效运算减少40%以上。
2. 精准模拟如何化解"试错成本"困局?
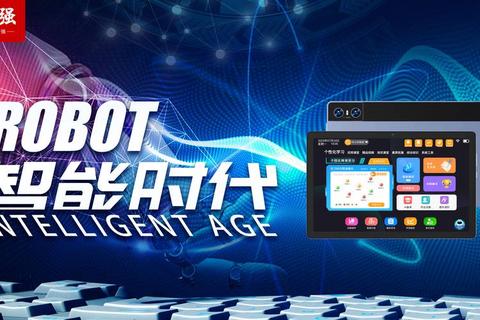
波音787客机研发过程中,因起落架液压系统故障导致的延期损失高达40亿美元。这种巨额试错成本在制造业绝非个例。智能革新西门子仿真软件:高效能精准模拟驱动工业未来,通过构建数字孪生体,正在改写这个剧本。上海电气在核电站冷却系统设计中,运用NX Simcenter解决方案,在虚拟环境中模拟了12种极端工况,提前发现3处潜在泄露风险,避免可能造成的数十亿元损失。
医疗设备领域更印证了这种变革的迫切性。美敦力公司开发新型心脏支架时,利用西门子Simcenter Flotherm软件进行血流动力学模拟。传统物理实验需要制作200多个原型,而数字化仿真仅用17个迭代方案就达到临床标准,开发周期压缩60%,材料浪费减少75%。这种"虚拟临床试验"的突破,让产品上市时间平均提前9个月。
3. 跨学科协同能否突破行业壁垒?
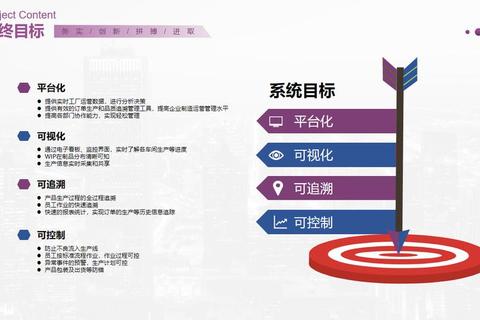
当新能源汽车的电机噪音与车体振动产生耦合效应,传统分科治之的仿真方式就暴露出局限性。某国产电动车企曾因此遭遇量产延迟,声学团队与结构团队的数据偏差导致重复修改6次模具。智能革新西门子仿真软件:高效能精准模拟驱动工业未来,通过多物理场耦合技术,正在打通这些行业藩篱。
东京地铁公司维护团队的故事最具说服力。他们将轨道振动数据导入Simcenter 3D软件,结合建筑结构模型,准确预测了地铁沿线写字楼的共振风险。这种将机械仿真与建筑力学结合的跨学科应用,使预防性维护效率提升3倍,相关事故率下降67%。更值得关注的是,软件内置的AI诊断模块,能自动识别92%的异常数据模式,让工程师可以聚焦最关键8%的复杂问题。
【行动指南】
对于计划进行数字化转型的企业,建议分三步部署:首先建立包含30%实测数据的基准模型库,通过6个月的数据积累校准算法;其次开展跨部门仿真技能培训,重点培养既懂工艺又通软件的复合型人才;最后构建迭代优化机制,每季度将实际生产数据反哺仿真系统,形成持续进化的数字孪生体系。正如宝马集团数字化总监施密特所说:"未来的工厂竞争,本质上是虚拟空间里的模拟精度之战。"当智能革新西门子仿真软件:高效能精准模拟驱动工业未来成为标配,那些提前构建数字优势的企业,必将在新一轮工业革命中占据先机。