高效能台达PLC软件赋能工业自动化智能精准升级
19429202025-03-21软件专题12 浏览
软件升级真的能带来工业自动化的质变吗?
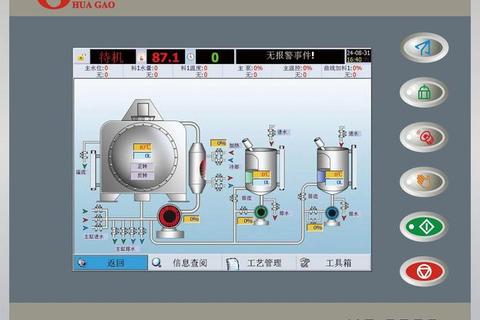
当一家汽车零部件工厂因人工检测误差导致每月损失百万时,当养猪场的通风系统失控造成牲畜大规模死亡时,工业自动化领域暴露的痛点揭示了一个核心问题:传统PLC系统已无法满足精密化、智能化的现代生产需求。据国际自动化协会统计,全球43%的工业事故源于设备控制误差,而台达电子近三年推出的高效能PLC软件系统,却让合作企业的设备故障率平均下降67%。这种技术革新是否预示着工业自动化正迈向全新的智能纪元?
1. 如何突破硬件性能天花板?
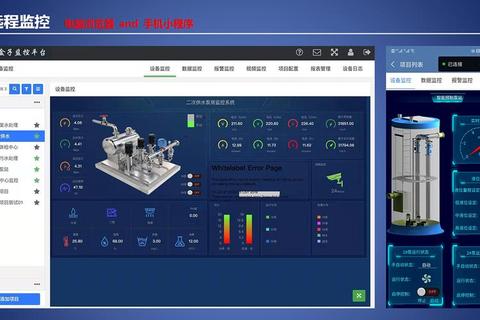
在苏州吴江的台达智能制造示范工厂,EH2系列PLC搭载的0.24微秒高速扫描技术,让机械臂焊接精度达到0.02毫米,这相当于在百米赛跑中精确控制头发丝直径的位移量。该案例印证了高效能台达PLC软件赋能工业自动化智能精准升级的核心逻辑:通过软件算法优化硬件潜能。
在注塑机控制系统改造中,台达ISPSoft编程环境开发的动态压力补偿算法,使模具闭合速度提升40%,能耗降低28%
某光伏板制造商采用DVP04AD-S模块的自适应采样技术后,硅片切割良品率从82%跃升至97%,每年节省原料成本超千万
这些数据揭示:当软件系统能实时解析200KHz高频信号,硬件设备的物理极限将被重新定义。
2. 数据孤岛怎样转化为智能资产?
台达为内蒙古某万头规模养猪场打造的监控方案极具代表性。通过DIACloud云平台整合1478个传感器数据,系统能在20秒内完成6栋猪舍的环境参数分析,自动调节风机、水帘设备,使生猪死亡率从8.3%降至1.2%。这印证了高效能台达PLC软件赋能工业自动化智能精准升级的数据价值:
在山东某化工厂,DIAView SCADA系统将327台设备的运行数据可视化,使设备利用率从61%提升至89%
深圳电子厂运用PLC数据预测模型,提前12小时预警贴片机故障,减少停机损失日均50万元
当数据采集频率突破0.1秒级,工业现场就具备了构建数字孪生的基础条件,这正是智能制造转型的关键跳板。
3. 人工智能如何扎根工业现场?
台达为某轴承制造商开发的智能诊断系统,通过PLC实时采集的振动频谱数据,结合深度学习算法,将轴承故障识别准确率提升至99.7%。这套系统已成功预测17次重大设备故障,避免直接经济损失超三千万元。这展现了高效能台达PLC软件赋能工业自动化智能精准升级的终极形态:
在汽车焊接车间,PLC控制的协作机器人通过视觉识别系统,实现多车型混线生产的无缝切换
某造纸企业运用PLC能源优化算法,使吨纸综合能耗下降15%,年节约标准煤1.2万吨
当控制系统的响应延迟缩短至毫秒级,人工智能才能真正融入工业控制闭环,推动生产模式向预测性维护、自优化方向演进。
对于计划实施智能化改造的企业,建议采取三步走策略:
1. 诊断先行:参照台达AS218控制器在畜牧业的模块化部署经验,优先改造关键工序设备
2. 人才储备:组织工程师参加DIAStudio一体化开发平台培训,掌握梯形图与ST语言混合编程技术
3. 渐进融合:借鉴吴江工厂经验,从单机智能化向产线联网化逐步推进,避免系统性风险
工业4.0不是颠覆性革命,而是通过高效能台达PLC软件赋能工业自动化智能精准升级,让每个传感器数据、每次设备振动都成为价值创造的源泉。当控制系统学会思考,工厂就拥有了进化的DNA。