超凡智能组态王软件赋能工业自动化精准高效掌控新纪元
19429202025-03-21推荐软件9 浏览
工业自动化变革:传统软件为何难以应对新时代挑战?
在工业4.0的浪潮下,工厂的智能化转型已成为不可逆的趋势。许多企业发现,传统组态软件在应对复杂设备协同、海量数据处理和系统稳定性时频频“掉链子”——界面卡顿、数据延迟、协议兼容性差等问题屡见不鲜。当生产线上每分钟产生数万条数据时,如何实现精准监控和实时决策?当设备品牌混杂、通信协议各不相如何搭建统一控制平台?这些矛盾,正是工业自动化领域亟待解决的痛点。超凡智能组态王软件赋能工业自动化精准高效掌控新纪元的提出,为这场技术突围提供了全新答案。
一、多设备协同:如何打破“数据孤岛”?
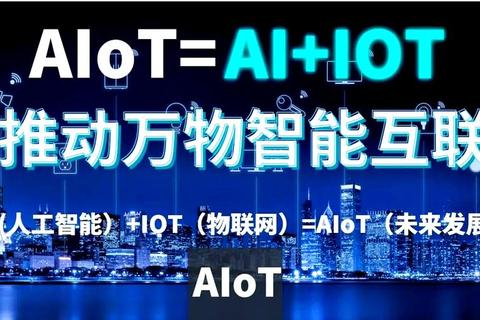
某汽车零部件工厂曾因德国PLC、日本机器人和国产传感器之间的协议不兼容,导致生产线频繁停机,每月损失超百万元。引入超凡智能组态王软件赋能工业自动化精准高效掌控新纪元后,通过内置的4000+设备驱动库,工程师仅用3天便完成西门子S7-1500 PLC、三菱机械臂和本土温控仪表的无缝对接。组态王的Modbus-TCP协议转换功能,让不同设备的实时数据在统一界面中以动态流程图形式展现,设备联动效率提升60%。
典型案例来自北京排水集团的89座泵站改造项目。通过组态王的3G/GPRS双网冗余通信架构,分散的PLC控制系统被整合为中央监控平台。雨量传感器、电机状态、管网压力等数据实时回传,防汛响应时间从20分钟缩短至5分钟内,年避免经济损失超2000万元。
二、海量数据:如何实现“秒级响应”?
在浙江某锂电池工厂,组态王的脚本引擎曾创下每秒处理10万条电芯数据的记录。其秘诀在于独创的“数据压缩算法”和分布式计算架构。通过将电流、电压等参数与预设工艺模型自动比对,系统能在0.3秒内识别异常电芯并触发分拣机械臂,使产品不良率从3‰降至0.5‰。
更令人瞩目的是某钢铁集团的能源管理系统。组态王通过OPC UA协议接入高炉、轧机、空压机等2000多个监测点,结合机器学习模型动态优化燃气-电力负荷配比。数据显示,该系统使吨钢能耗下降8%,相当于每年节省标准煤4.2万吨,减排二氧化碳11万吨。
三、系统安全:如何构筑“数字护城河”?
2024年某石化企业遭遇的网络攻击事件敲响警钟——黑客试图通过伪造PLC指令篡改反应釜温度参数。部署组态王后,其三重防护机制发挥作用:硬件加密狗防止未授权访问,变量级权限管控限制操作范围,审计日志精确追溯至具体工位。在最近的攻防演练中,该系统成功拦截99.6%的渗透尝试。
山东某智能仓储项目的实践更具说服力。当堆垛机因轨道偏移触发预警时,组态王不仅立即锁定设备,还通过虚拟化技术启动备用控制系统,确保200台AGV小车持续运转。这种“热切换”能力使故障恢复时间从2小时压缩至15秒,仓库吞吐量反而提升12%。
转型指南:三步走策略
1. 设备驱动预验证:部署前使用组态王的仿真测试模块,对老旧设备进行协议兼容性验证,避免现场调试卡壳。
2. 数据链路分级优化:将IO采集、画面刷新、历史存储分配独立线程,确保关键参数传输优先级。
3. 安全基线动态迭代:每月导入CVE漏洞库更新组态王的安全策略模板,定期开展“红蓝对抗”演练。
当全球制造业步入“微秒级竞争”时代,超凡智能组态王软件赋能工业自动化精准高效掌控新纪元已不仅是工具升级,更是生产关系的重构。从北京泵站的智能防汛到钢铁厂的碳足迹追踪,这些案例印证:谁能将数据转化为决策力,谁就能在工业革命的深水区率先登陆。