智能革新全维度精准加工中心模拟仿真软件高效实践平台
19429202025-03-25推荐软件13 浏览
虚拟加工能否终结传统制造的“试错成本”?
在制造业数字化转型的浪潮中,一个争议性问题始终萦绕在从业者心头:高昂的试错成本是否已成为制约行业发展的最大瓶颈?
据统计,传统加工中因程序错误导致的刀具碰撞、材料浪费等问题,平均每年造成企业10%-15%的成本损失。而随着智能革新全维度精准加工中心模拟仿真软件高效实践平台(以下简称“全维度平台”)的崛起,这一难题正迎来颠覆性解决方案。从虚拟刀轨预测到实时碰撞检测,从多轴联动仿真到工艺参数优化,该平台如何重构制造业的底层逻辑?我们通过三个核心维度展开分析。
一、虚拟仿真如何替代“真金白银”的试错?
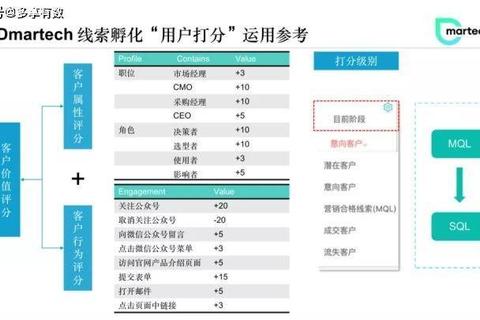
在浙江某精密模具厂的案例中,工程师曾因一个五轴联动加工程序的微小误差,导致价值20万元的钛合金工件报废。而引入全维度平台后,类似风险被提前化解。
该平台通过多轴加工仿真技术,可在虚拟环境中完整复现机床运动轨迹、刀具切削状态和材料去除过程。例如,某汽车零部件企业使用平台内置的FANUC系统模型,在加工曲轴前通过仿真发现了两处潜在的刀具干涉点,仅耗时2小时便完成程序修正,避免了12万元的材料损失。更值得关注的是,其三维实时切削技术能精确模拟不同刀具(如Φ12端铣刀与Φ8铰刀)的切削力变化,帮助优化进给量参数,使某铝合金零件的加工效率提升38%。
二、人才培养能否告别“纸上谈兵”?
宁波智能制造专家委员会的调研显示,传统数控操作员培养周期长达6-12个月,且实操训练受设备限制严重。全维度平台正通过沉浸式实训模式破解这一困局。
以深圳某职业院校为例,其将宇龙数控仿真系统集成至教学体系,学生可在虚拟环境中完成从毛坯装夹到G代码校验的全流程操作。平台提供的16种数控系统模型(包括华中数控与广州数控),使学员适应不同工厂设备的周期缩短60%。更突破性的是,平台新增的AI智能问答功能,可实时解答学员关于刀具选型、坐标系设置等问题,相当于配备24小时在线的“虚拟导师”。某刀具制造企业反馈,经过平台培训的新员工上岗首月产品合格率即达92%,远超传统培训模式的78%。
三、数据驱动如何优化生产全流程?
山东某航空航天部件制造商曾面临工艺参数优化的困境:20人的工艺团队每月仅能完成3种复杂零件的参数迭代。接入全维度平台后,这一效率发生质变。
平台集成的DeepSeek-V3算法模型,可基于历史加工数据自动生成刀具路径优化方案。在钛合金叶轮加工案例中,系统通过分析2000组切削参数,推荐将主轴转速从8000r/min调整至8500r/min、径向切深从0.2mm增至0.25mm,使单件加工时间减少22分钟,年产能提升1500件。其智能报表系统可自动生成班组效率排名、刀具损耗趋势等数据,某电子企业借此将设备综合效率(OEE)从68%提升至83%。
从工具升级到生态重构的实践路径
全维度平台的价值已超越单一软件范畴,正在构建“仿真-优化-决策”的制造新生态。对于不同规模的企业,建议采取差异化策略:
1. 中小型企业可优先部署基础仿真模块,重点利用碰撞检测与刀轨优化功能,预计首年可回收80%投入成本;
2. 大型制造商应建立数字孪生系统,将平台与MES、PLM系统集成,实现工艺参数与生产计划的动态联动;
3. 教育机构需构建“虚拟机床+真实设备”的混合实训体系,通过平台降低60%的实训耗材成本。
当制造精度进入微米级竞争时代,智能革新全维度精准加工中心模拟仿真软件高效实践平台已不仅是风险控制的“保险栓”,更是企业降本增效的“加速器”。正如工业富联观澜工厂的实践所证:真正的智能制造,始于对每个切削参数的极致模拟。